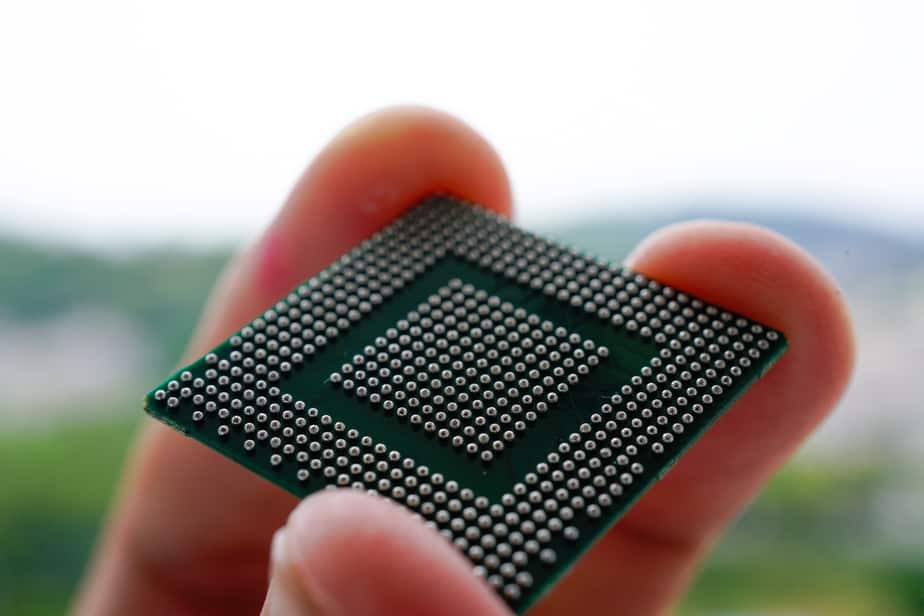
There are several different elements of the PCB assembly process to bring your product to life, one of these being the BGA process (ball grid array), which broadly covers the process of surface mounting components onto your PCB.
What is BGA?
Ball grid array (BGA) is a type of surface mount packaging that is mainly used for integrated circuits. Ball Grid Array is a small package that allows high density connections to be made easily, which is why they work so well for integrated circuits. Ball grid array uses the underside of the package, rather than the sides or edges like other packages such as the quad flat package, this allows more space for pins for connections to be made on the board.
Ball grid array gets its name due to the placement of the pins on the board, which are placed in a grid pattern. On other packages, standard pins are used, however, ball grid array have small pads with balls of solder underneath. These balls are used to make connections using precise placement and soldering techniques.
There are several different types of ball grid array packaging used within the BGA process by manufacturers, however, the most commonly used are plastic ball grid array, ceramic ball grid array and tape ball grid array.
Plastic ball grid arrays are the most common, made of PCB material like resin with an overmolded layer of plastic. Ceramic ball grid arrays follow closely, in this packaging the die is attached to the surface with a ceramic multilayer. The ceramic ball grid arrays use high temperature solder balls which do not melt during the reflow process. Lastly are tape ball grid arrays, which are the newest to the industry but still popular. This consists of die attached to a flexible circuit or tape that has a metal layer on either side, these two layers of metal allow for connection from the die to the array of solder balls.
Ball grid array packaging has become increasingly popular over the years, this is due to a number of advantages it holds. One of these is their superlative thermal dissipation capability, which allows heat generated by the integrated circuit (IC) to be conducted out of the device, meaning it is kept cool while operating, thus leading to a longer shelf life. Ball grid array packaging also supports higher pin counts compared to other packages, meaning more connectivity throughout the board alongside more space on the PCB for other functionalities. The ‘pins’ on this particular packaging being small balls bring an added advantage, there are no broken or bent pins that may occur on other packages.
Additionally, the interconnections on the PCB are shorter, resulting in improved electrical conductivity.
All of these qualities mean that ball grid array packaging is most cost effective whilst also offering higher performance results.
What is the BGA rework process
Ball grid arrays help with precision and for the board to have extra space to efficiently and accurately mount components. As technology advances there is a demand for PCBs to become smaller, but still have the same results and quality. The process of mounting components on PCBs with precision is extremely important, it can be done either with through hole technology or surface mounting. The BGA process is one technique used in surface mounting and comes into play when some components on the board need to be reworked, removed or replaced.
There are several steps to this process, outlined below.
Bake the PCB
In order to begin the removal or replacement of components on the board, the PCB must be heated until the solder becomes molten. This is known as reflowing soldering, which is a technique wherein the PCB is brought to a fixed temperature to melt the solder balls.
Once this has been done the PCB will be removed by a vacuum. The heat is applied to the component that needs to be removed, but without spreading to the rest of the conductive material of the PCB, the heat needs to remain localised on the top side near the component.
Remove the BGA
Once the PCB has been preheated, the component is then lifted from the PCB using a vacuum. If the previous step of pre-heating has not been completed carefully, it can be extremely difficult (and expensive) to remove the BGA, or you may not be able to salvage or remove it at all.
Bake the BGA
In order to remove any residual solder, the PCB needs to be preheated and the vacuum used again to remove any residue. Before this is done your PCB must be cleaned, which is done through monitoring air or nitrogen flow to liquefy the solder. Once the preheating has begun the vacuum is then used to remove the solder, if however there are several components on the board, this can be tricky. In this scenario it is important to closely control the temperature and volume of air in the vacuum to ensure other components are not damaged.
Site Dress the BGA
Before any new ball grid arrays are placed onto the device, it must be cleaned again to ensure the removal of any excess residue. Ball grid arrays can often be expensive, so manufacturers don’t always want to disregard those they are removing. One method to help preserve them would be to remove them using a stencil method which allows a solder ball to fall through and as the remaining openings fill up, excess solders are swept off the stencil and can be preserved and potentially used again for another component.
BGA re-soldering and attachment
In order to re solder and attach the new BGA package you need to apply flux paste on to the pad, which will help solder balls stick. Once you have applied these older palls you can put the same paste onto the bottom of the BGA package and place it on the solder balls.
This step is then similar to removing the initial device from the PCB using heat which then allows the soldering and reattachment to take place.
If you are interested in finding out more on the BGA rework and process, or need a tailored BGA service for your business, get in touch for a free quote.