The Circuit Board Protective Coating and Finish Process
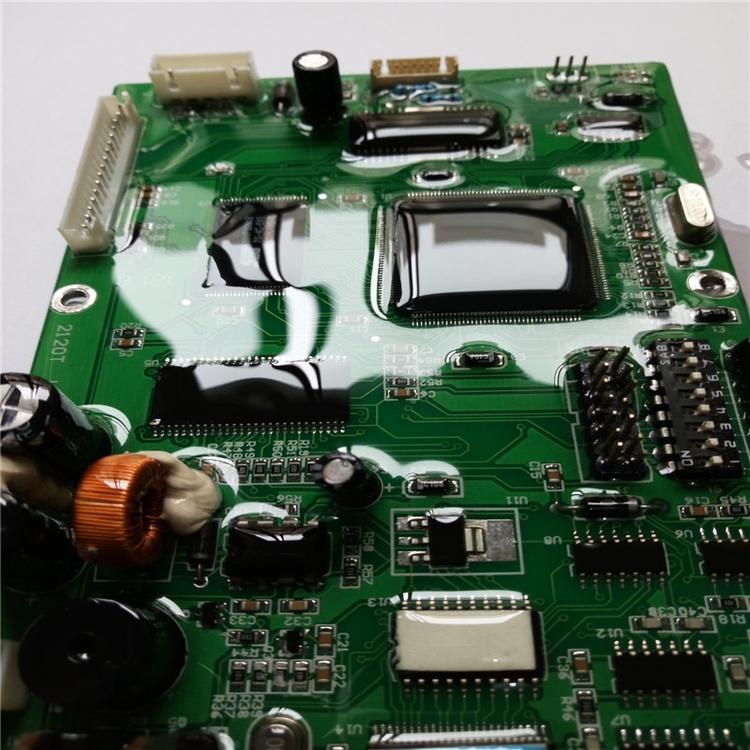
What is protective finishing for PCBs?
A PCB surface finish is a layer of metal applied in between the bare area of your board, and the solderable pads and components of your PCB. It’s an important part of the PCB assembly process, as PCB surface finish allows boards to have a longer shelf life by protecting them from oxidation and corrosion. The PCB surface finish refers to the process of artificially forming a layer on the PCB board. Applying a PCB surface finish allows boards to withstand high temperatures and any thermal demands and pressures, alongside ensuring good solderability of electrical properties for the PCB. Without this finish and protection, the pure copper metal of the board is left exposed and will be easily susceptible to oxidation, corrosion and deterioration. If the surface of the board has not been treated with a surface finish, it can be near impossible to solder components, thus rendering the board inoperative.
In order to ensure your PCB and product is sustainable, particularly under harsh or testing conditions, it’s important the board goes through the process of a surface finish.
What types of coating can you choose from?
There are several different kinds of protective coating which can be used during the process, generally being made from a range of metallic materials. This blog will discuss some of the most common types of surface finishes, including those used by ABL circuits in the assembly process. It’s important to ensure you select the correct surface finish for your board, as surface mounts have advanced and become more complex, alongside industry standards and regulations. When choosing your surface finish for your PCB board, there are a few things you should consider, including the component type you’re working with, cost effectiveness, reworkability and whether you’re using a lead or a lead free surface finish.
HASL
For decades, HASL has been one of the most popular surface finish choices. HASL stands for Hot Air Soldering Level and is a conventional surface finish wherein the board is dipped into a molten solder bath in order to cover all exposed copper. The surface of the PCB is then flattened with heated compressed air to form a coating layer that resists any copper oxidation and creates a reliable base for soldering. Any surplus solder is removed by passing the board between hot air knives.
Since the introduction of restrictions of hazardous substances (RoHS), lead free HASL should always be used. ***At Ruiputuo,we always use lead free HASL.***
HASL has several advantages, including:
It’s cost effective
It’s widely available
It’s eco friendly
It provides superior wetting during component solderinga
It has a relatively long shelf life
However, some of the disadvantages include HASL not being suitable for fine pitch components or high density intersurface products, and lead free HASL can also result in uneven surfaces across the board.
OSP
OSP coating (Organic Solderability Preservatives) is an organic surface finish which is water based and predominantly used on copper pads. OSP is sprayed onto the copper pads to provide a protective film prior to soldering.
OSP protective coating for PCBs is generally not as robust as HASL and can be very sensitive when handling. Additionally, its shelf life is not as long as that of HASL, which makes it more suited for prototypes. Historically, OSP was a simple and affordable method of protective coating, however, in recent years due to the low demand, ENIG has become the standard even when prototyping.
ENIG
ENIG (Electroless Nickel Immersion Gold) is becoming one of the most popular protective coating methods in the PCB world and is widely used. ENIG consists of two metallic layers, the first being nickel which is placed directly onto the copper. A layer of gold is then used to protect the copper from oxidation. ENIG has become popular due to the increase in two trends within the industry; lead free requirements and the rise of flat surface components, which are two of ENIG’s strong points.
There has been an increase in the complexity of PCB design and components, such as BGAs and ever smaller components, which has led to a growth in ENIG demand. Additionally, ENIG creates an incredibly durable surface finish which gives PCBs a long shelf life and makes it ideal for high quality PCB manufacture and assembly.
The downfall to ENIG comes when looking at costs, due to the raw materials used, such as gold. The process of protective coating with ENIG can also be more complex than that of OSP and HASL, and therefore more labour intensive.
What coating does Ruiputuo use and why?
At Ruiputuo we are very meticulous about the processes and materials we use to ensure we’re creating the best quality products for our PCBs and customers.
While there are several different coatings and processes available for us to undertake when it comes to protective coating, as a business we made the executive decision to move away from using silver coating.
While ENIG can be a more expensive process, the financial differences between ENIG and OSP is comparatively small, but the results are vastly different. ENIG provides a higher quality finish, as highlighted above, including a durable surface. Moreover, ENIG provides a higher quality finish due to the use of gold, as the silver coating used in finishes such as OSP do eventually oxidise after time. This leads to a poor solder joint when assembled and thus rendering the board less durable.
ENIG is recommended when working with fine pitch components such as BGA, QFN and DFNs, as the plating process leaves a near perfectly smooth surface.
At Ruiputuo we also use HASL in the PCB assembly process, which leaves a slightly dome shaped pad with its finish.
HASL is used when we’re working with through hole components rather than fine pitch components, as HASL is just as effective whilst saving on costs not using gold materials, such as with ENIG.
Where to get more support?
If you would like to find out more about the protective coating process, and which finish would be best suited for your board, get in touch with one of our specialists for a free quote.