It’s what’s on the inside that counts” is a message many of us are taught at a young age, and it is an important one. Why? Often, the inner workings of something (be that a person or object) is more important than anything external. However, it’s a mistake to think that the “outside” doesn’t matter. In all walks of life, it can be impossible to escape the appeal of a beautifully wrapped gift or a nice outfit, for example.
Whoever coined that phrase likely didn’t have PCB enclosure design in their mind when doing so. While the enclosure is likely to receive far fewer resources during product development than the PCB due to the latter being a far more involved process, a poor enclosure can rapidly inhibit an electronic device’s performance and service life. Therefore, optimization of any PCB design must also extend to its enclosure.
Enclosure type | Description | Advantages | Sub-types |
Racks | Vertical, floor-dwelling unit. Often contains front and rear access with side panels dedicated to ventilation. | Typically does not require additional mounting, aiding in deployment and reuse. |
|
Cabinets | Smaller and shallower than racks, cabinets allow for ease of wall mounting or general portability. | Lightweight and sturdy cabinets can be used where enclosure volume is less of a concern than neighboring equipment. |
|
Chassis | Simple 5- or 6-sided coverage for electronics. | Can be used as a sub-enclosure for larger rack designs. A variety of customization options from material to shape and size. |
|
Thermal Performance is at the Core of Enclosure Design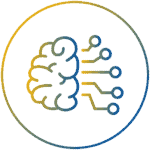
The design of a PCB enclosure has to balance many performance factors of the board. While the physical size and shape of the board is the primary driver of the type of enclosure available, thermal concerns are the highest priority. Heat not only causes poor performance and interruption to function, but it acts as an aging factor for board materials. Therefore, a strong enclosure design will eliminate heat and improve the long-term viability of the board.
When discussing the thermal design of the enclosure, there are a few considerations to keep in mind. While heat has three main vectors of dissipation – conduction, radiation, and convection – it is convection that engineers can utilize to the greatest cooling effect. Of the other methods of heat dissipation, radiation offers minimal cooling potential. Still, conduction can be combined with convection to effectively move heat from points of generation to areas of more accessible airflow (this is a cornerstone of thermal routing). Convection itself can be further subdivided into its level of energy input required to facilitate heat transfer:
Passive cooling occurs when no additional input is required for convection to operate automatically.
Active cooling is required when the temperature gradient between the components and ambient air temperature is insufficient for spontaneous cooling.
It’s important to recognize the gradient is the measure of effective cooling. Components running hot in a cold environment would not require additional input because the difference between component temperature and surroundings is significant. On the other hand, there may not be a large enough potential difference between a component running only at a moderate temperature and a warmer environment, or the air surrounding the enclosure quickly becomes thermally saturated and can no longer provide cooling.
In these cases, the passive cooling design must be supplemented with active measures that better circulate the air and drop the surrounding temperature. Regardless of the exact implementation of convection cooling, designers should create enclosures that enable cross ventilation through the sides of the enclosure and at the top and bottom of the enclosure for exfiltration of warmer air out due to its lower pressure.
Additional Enclosure Factors to Maximize Suitability
Enclosure design will also need to aid electronics by contributing positively to the external features of the board. Foremost will be the wire harness where it is applicable: electronics can feature several wires, cables, and connections for off-board communications and larger system integration. Enclosures should help manage the physical routing of these cable networks to prevent damage to strained wires while enabling ease of access and troubleshooting. The classic modern example is the computer desk or home AV setup with multiple wires running in different directions. At the same time, this is merely unsightly in small doses, a server rack running multiple CAT6/7 cables will want to bundle and mount these together to prevent time loss during maintenance or unit replacement.
Building on cable assembly, flex printed circuits can also be an option for extremely small form factors (think wearable electronics) or space-restricted enclosures. Flex circuit(s) can replace hundreds of connections with a thin profile that can fold and bend to maximize the amount of 3D space available.
An enclosure framework also acts as a physical space to route cables with EMI emission/susceptibility concerns at a distance to prevent coupling, noise, crosstalk, etc. This feature can be further extended into a Faraday cage/shield for blocking unwanted EMI emissions into and out of the enclosure when the time for a revision is constrained, and a board is not expected to pass EMI laboratory testing.
Finally, enclosure design will want to account for the needs of access and scalability of the electronics to the system. Common enclosure access can include front and rear doors; instead of removing electronics from the enclosure for access to a particular face of the device, technicians can easily access either face. Further support for enclosure access can include removable side panels that normally allow for sufficient airflow while minimizing particulate buildup inside the enclosure. As for scalability, not only can individual enclosures support system growth with compartmentalized and expandable storage, multiple enclosures can be combined in a modular fashion for semi-customized enclosure solutions.
Don’t Get Boxed In by Design: Contact Your Contract Manufacturer
Enclosure design is a less heralded aspect of electronics products, but it serves various important functions all the same. Designers will want to carefully weigh the pros and cons of enclosure styles to find the system that maximizes the performance of the electronics system. It may be the case that an off-the-shelf enclosure lacks the robustness necessary for a particular job; in these cases, a custom build can better address the specific requirements.
At Ruiputuo, we’re a team of engineers committed to building electronics for our customers. That dedication extends to offering well-engineered enclosures that can meet the expectations of their deployed operating environment. Combined with our valued manufacturing partners, we produce high-quality PCBs and supporting equipment in several life-saving and life-changing industries.